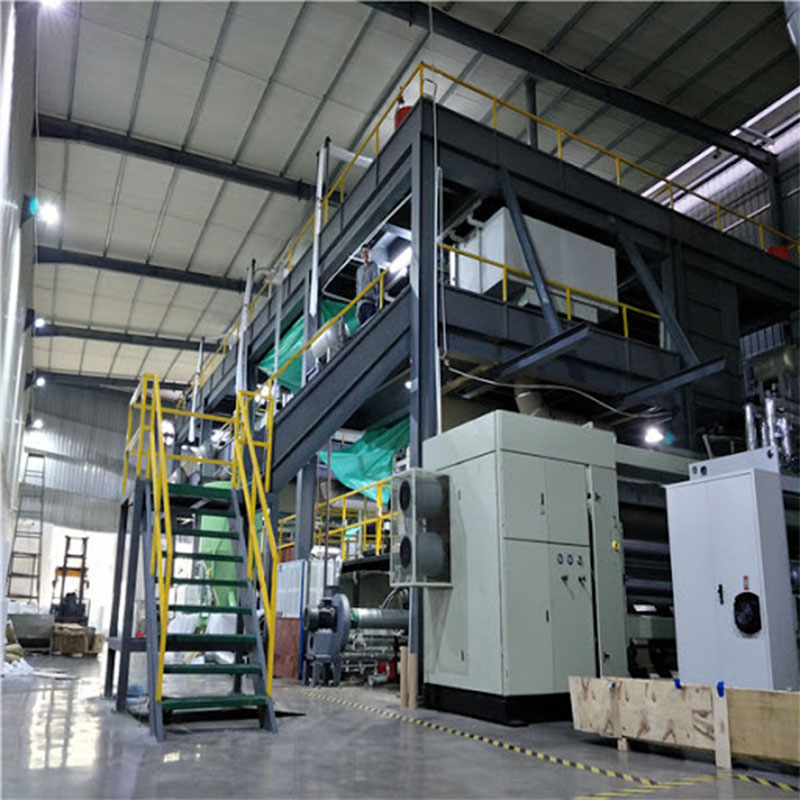
Introduction: Innovations in Spunbonded Nonwovens
The world of nonwoven fabrics has seen a surge in demand due to their adaptability, resilience, and cost-effectiveness. Among these, SSS spunbond composite fabrics stand out as a groundbreaking innovation, transforming the industry through advanced manufacturing processes. This article delves into the intricate specifications and vital components of GLNON’s pioneering spunbonded nonwoven production line, emphasizing the groundbreaking strides in SSS composite fabric production.
Exploring the Specifications of GLNON’s Cutting-Edge Production Line
ГЛНОН, a prominent Chinese manufacturer renowned for its expertise in nonwoven machinery and a substantial presence in Southeast Asia and the Middle East, leads the way in producing high-quality spunbonded nonwoven machines. Our spunbonded nonwovens production lines come in variable widths of 1600mm, 2400мм, and 3200mm, adaptable to diverse manufacturing needs, with equipment dimensions scaling from 31x13x11m to 34x15x11m respectively.
The production line boasts three sets of precision-engineered spunbond die heads, ensuring the fabrication of fabrics with filament deniers ranging from ≤1.7-2.0den (С) to 2-4μm (М), thereby facilitating a range of fabric attributes. With a fabric weight capability stretching from 10g/m² to 150g/m², GLNON nonwoven fabrics production lines accommodate a myriad of applications. Furthermore, they operate at remarkable speeds of 350m to 450m per minute, with an annual production capacity reaching 4500 тонны, fulfilling the rigorous demands of numerous industries. Notably, the SSS production process maintains an impressively low energy consumption of less than 800-1000 kWh per ton.
Key Components Fueling Efficiency and Productivity
At the core of GLNON’s production lines lie two pivotal components that elevate operational efficiency:
Advanced Electrical Control Cabinet: This cabinet harnesses AC frequency modulation for meticulous control over production variables, enabling instant adjustments to speed, tension, and more, ensuring consistent, premium fabric output. Its fully digitized communication system promotes seamless coordination along the production chain, maximizing overall efficiency.
Sophisticated Spinning Drafting System: Central to fabric uniformity and quality, this system meticulously arranges and aligns filaments during production, employing sophisticated drafting techniques and intelligent algorithms to optimize fiber distribution and strength. The result is nonwovens with unparalleled tensile strength, tear resistance, and durability.
The Advantages of SSS Spunbond Composite Fabric Production
The advent of SSS technology brings forth a new era in nonwoven fabrics, characterized by:
Superior Fabric Characteristics: The three-layer SSS structure bolsters fabric strength, stability, and overall performance. By combining various filament deniers, SSS composites can be tailored for specific attributes like softness, воздухопроницаемость, and fluid repellency, expanding application scope.
Optimal Resource Use: The SSS process strategically optimizes raw material usage across three distinct layers, minimizing waste and maximizing productivity.
Extensive Application Versatility: From hygiene and medical products to geotextiles, фильтрация, and automotive sectors, SSS spunbond composites prove invaluable where durability, strength, and performance are paramount.
Economical Production: The SSS process couples rapid production rates with resource efficiency, offering a cost-effective alternative to conventional methods.
Conclusion: GLNON’s Global Impact and Invitation to Collaborate
The progression in spunbonded nonwovens, exemplified by GLNON’s SSS composite technology, paves the way for an industry capable of addressing a broader spectrum of needs with enhanced fabrics. The sophisticated specifications and advantages of SSS spunbond composites empower manufacturers to navigate the evolving demands of diverse sectors with precision and efficacy. GLNON’s global footprint, particularly in Southeast Asia, the Middle East, and with significant exports to India, attests to its commitment to excellence. We warmly invite inquiries, promising comprehensive machine details and competitive wholesale pricing from our dedicated team.