Nonwoven fabrics have become an integral part of various industries, including healthcare, hygiene, agriculture, and automotive. These fabrics offer versatility, durability, and cost-effectiveness, making them highly sought after. One of the key technologies driving the production of nonwoven fabrics is the SMS spunmelt machine. This article explores the significance of SMS spunmelt machines and their impact on nonwoven fabric manufacturing.
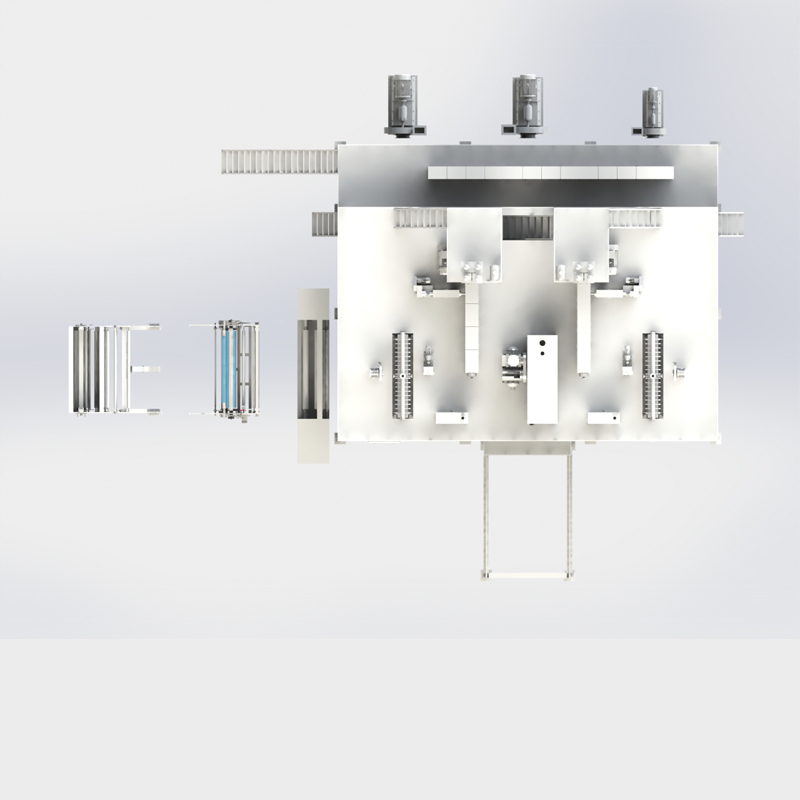
Understanding SMS Spunmelt Machines
SMS stands for “Spunbond-Meltblown-Spunbond,” which refers to the three-layered structure of nonwoven fabrics produced by these machines. SMS spunmelt machines combine the processes of spunbonding and meltblowing to create a composite fabric with enhanced properties. The spunbond layer provides strength and stability, while the meltblown layer adds filtration and barrier properties.
The Role of SMS Spunmelt Machines
SMS spunmelt machines play a crucial role in the production of high-quality nonwoven fabrics. They enable manufacturers to create fabrics with a wide range of characteristics, including different weights, thicknesses, and performance attributes. These fabrics find applications in various sectors, such as medical gowns, surgical masks, diapers, wipes, geotextiles, and automotive interiors.
Advantages of SMS Spunmelt Machines
SMS (Spunbond-Meltblown-Spunbond) spunmelt machines offer several advantages in the production of nonwoven fabrics. Here are some key advantages of SMS spunmelt machines:
- Versatility: SMS spunmelt machines allow for the production of a wide range of nonwoven fabrics with varying properties. The combination of spunbond and meltblown layers provides versatility in fabric weight, strength, barrier properties, and filtration efficiency. This makes SMS fabrics suitable for various applications such as medical and hygiene products, protective apparel, filtration media, and geotextiles.
- Enhanced Barrier Properties: The meltblown layer in SMS fabrics contributes to their excellent barrier properties. The fine microfibers created during the meltblown process create a dense web that can effectively block liquid droplets, particles, and even bacteria and viruses. This makes SMS fabrics ideal for medical gowns, surgical drapes, and other protective barriers.
- Superior Strength: SMS fabrics have enhanced tensile strength compared to single-layer spunbond or meltblown fabrics. The combination of both processes results in a fabric with improved tear resistance and durability. This makes SMS fabrics suitable for applications that require high strength, such as automotive and construction materials.
- Breathability: The spunbond layers in SMS fabrics provide breathability and comfort. The continuous filaments formed during the spunbond process create a porous structure that allows air and moisture vapor to pass through while maintaining the desired barrier properties. This makes SMS fabrics comfortable to wear and suitable for applications such as disposable hygiene products and breathable membranes.
- Efficient Production: SMS spunmelt machines offer efficient production capabilities. The integration of multiple processes into a single machine reduces the need for separate production lines, saving space, energy, and labor costs. Additionally, SMS production can be continuous, allowing for high-speed and large-scale production of nonwoven fabrics.
- Cost-effectiveness: SMS spunmelt technology can offer cost advantages compared to traditional fabric production methods. The integration of spinning, meltblowing, and bonding processes into a single machine streamlines production and reduces material waste. This results in improved efficiency and cost savings for manufacturers.
- Sustainability: SMS spunmelt machines can contribute to sustainability efforts. The ability to produce lightweight but strong fabrics with enhanced barrier properties can reduce material consumption. Additionally, the use of recyclable materials and the possibility of incorporating recycled content in SMS fabrics can promote a circular economy and reduce environmental impact.
Choosing the Right SMS Spunmelt Machine Supplier
When selecting an SMS spunmelt machine supplier, several factors should be considered
- Technology and Expertise: Look for a supplier with a proven track record in SMS spunmelt technology. They should have the expertise to provide reliable machines that meet industry standards and produce high-quality fabrics.
- Customization Options: Consider a supplier that offers customization options to meet specific production requirements. This includes the ability to adjust fabric weight, width, and other parameters to cater to diverse applications.
- After-Sales Support: A reputable supplier should provide comprehensive after-sales support, including installation, training, and maintenance services. This ensures smooth machine operation and minimizes downtime.
- Research and Development: Choose a supplier that invests in research and development to stay at the forefront of technology advancements. This ensures access to the latest innovations and continuous improvement in fabric quality and performance.
SMS spunmelt machines have revolutionized the nonwoven fabric industry by enabling the production of versatile, high-performance fabrics. These machines offer efficiency, customization options, and sustainability benefits. By partnering with a reliable SMS spunmelt machine supplier, manufacturers can enhance their production capabilities and meet the growing demand for nonwoven fabrics across various sectors.