In the realm of textile manufacturing, innovation and efficiency reign supreme. Spunbond nonwoven fabric making machines have revolutionized the industry, transforming the production of nonwoven fabrics with their advanced technology and versatility. In this comprehensive guide, we will delve into the world of spunbond nonwoven fabric making machines, exploring their intricate processes, key components, and the diverse applications of the fabrics they produce, driving progress across multiple sectors.
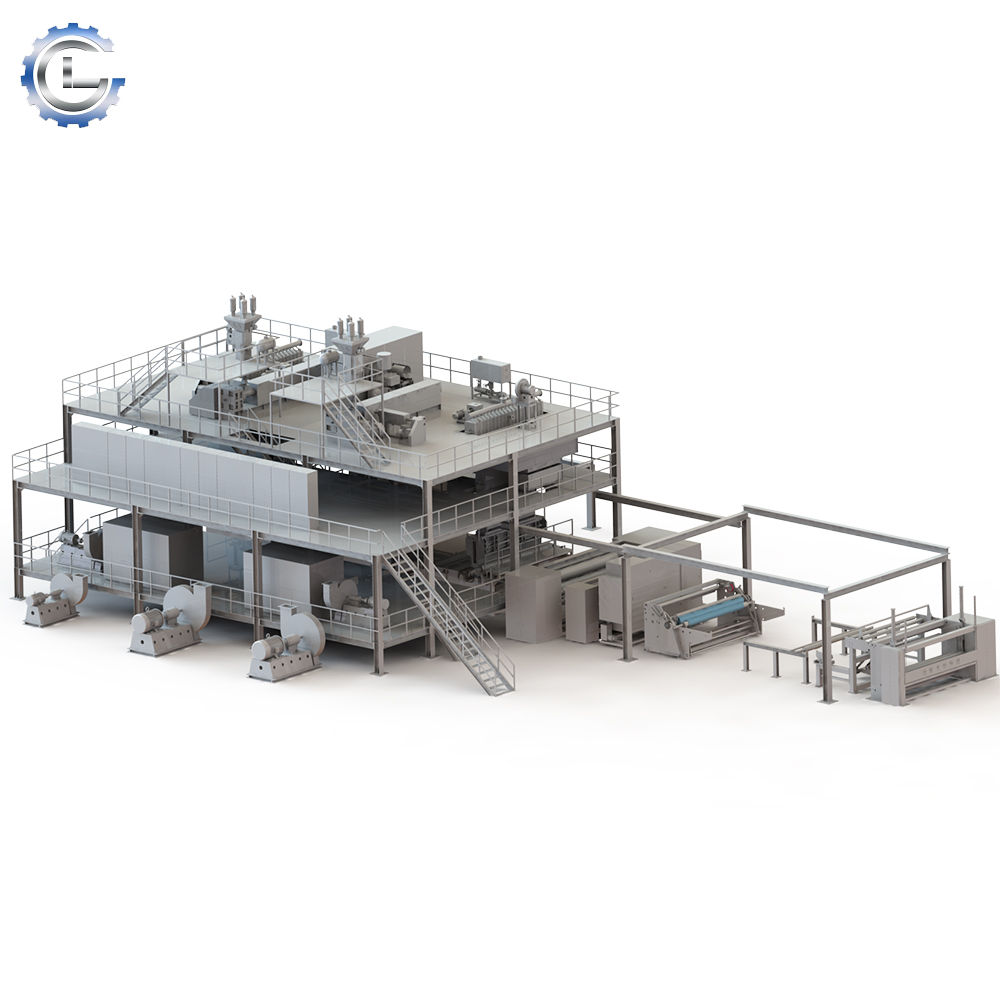
Understanding Spunbond Nonwoven Fabric Making Machines
Spunbond nonwoven fabric making machines employ a unique process to create nonwoven fabrics without the traditional weaving or knitting techniques. These machines utilize polypropylene or other thermoplastic polymers to produce continuous filaments that are bonded together to form a cohesive fabric structure.
Key Components Of Spunbond Nonwoven Fabric Making Machines:
- Polymer Extruder: The extruder melts the thermoplastic polymer, creating a molten polymer stream that is ready for fiber formation.
- Spinnerets: The molten polymer is forced through spinnerets, which contain tiny holes that shape the polymer into continuous filaments.
- Cooling System: The extruded filaments are rapidly cooled using air or water jets, solidifying them into fibers.
- Web Formation: The cooled fibers are drawn into a web, which is a continuous sheet of nonwoven fabric.
- Bonding: The web undergoes various bonding methods, such as thermal bonding or chemical bonding, to create a strong and cohesive fabric structure.
Advantages of Spunbond Nonwoven Fabrics:
- Strength and Durability: Spunbond nonwoven fabrics exhibit exceptional tensile strength and tear resistance, making them highly durable.
- Water-Resistant: The nonwoven structure of the fabric effectively repels water, making it suitable for applications where moisture resistance is crucial.
- Breathability: Despite its water-resistant nature, spunbond nonwoven fabric allows for air permeability, ensuring breathability and comfort in various applications.
- Lightweight and Flexible: The fabric’s lightweight and flexible nature makes it easy to handle, manipulate, and convert into different shapes and forms.
- Eco-Friendly: Spunbond nonwoven fabrics are recyclable and reusable, contributing to sustainable practices and reducing environmental impact.
Applications of Spunbond Nonwoven Fabrics:
The versatility of spunbond nonwoven fabrics has led to their widespread adoption across numerous industries:
- Medical and Healthcare: The fabric’s hygienic properties make it ideal for surgical gowns, face masks, disposable bed sheets, and other medical supplies.
- Hygiene and Personal Care: Spunbond nonwoven fabric is extensively used in baby diapers, feminine hygiene products, wet wipes, and disposable towels due to its softness, absorbency, and comfort.
- Agriculture: The fabric’s durability and water-resistant properties make it suitable for crop covers, weed control mats, and seedling bags, enhancing agricultural productivity.
- Packaging: Spunbond nonwoven fabric serves as a lightweight and eco-friendly packaging material for various products, including food, beverages, and consumer goods.
- Industrial Applications: The fabric’s strength and versatility make it useful in filtration systems, insulation materials, and protective clothing in industrial settings.
Spunbond nonwoven fabric making machines have revolutionized the textile industry with their ability to produce high-quality nonwoven fabrics efficiently and cost-effectively. The exceptional properties and diverse applications of spunbond nonwoven fabrics have made them indispensable in various sectors, driving innovation and sustainability. By embracing the power of spunbond nonwoven fabric making machines, businesses can unlock new possibilities and enhance their competitive advantage in the ever-evolving textile landscape.